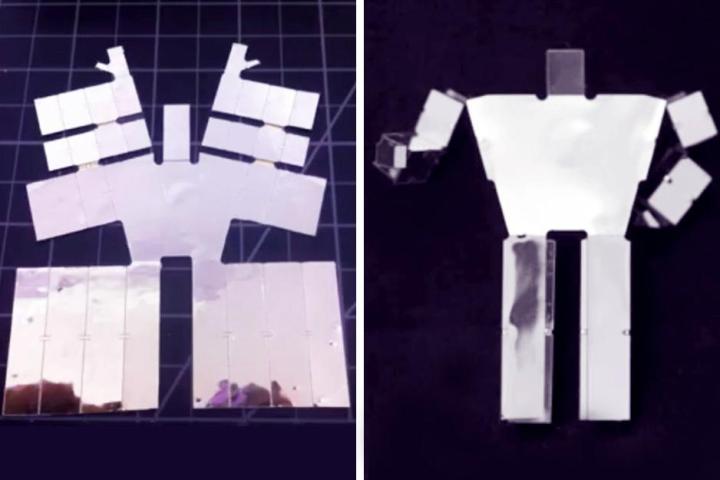
Want to build your very own robot? It turns out all you might need is a little heat.
Researchers from the Massachusetts Institute of Technology (MIT) have developed 3D-printed robots that can assemble themselves together after being exposed to heat. They demonstrated how these prototypes work in two new studies, to be presented at the 2014 IEEE International Conference on Robotics and Automation held in Hong Kong next week.
Using a type of polymer called polyvinyl chloride, or PVC, the research team led by Daniela Rus created two-dimensional sheets of the material and placed them between two rigid polyester films full of different sized slits. They noted that the position of the slits are important for controlling the angles at which the PVC sheets will fold.
Then, the sheets just need to be popped in the oven.
When the material is heated, the PVC contracts and the slits close, pressing the edges of the polyester film up against each other. These edge patterns ultimately direct the movement of the PVC and help to form the final 3D shape of the product.
Rus said the entire process is very complex, as all the slits and materials must move in sync in order to get the desired final shape.
“You’re doing this really complicated global control that moves every edge in the system at the same time,” Rus, an engineering and computer science professor at MIT, said in a statement. “You want to design those edges in such a way that the result of composing all these motions, which actually interfere with each other, leads to the correct geometric structure.”
One of the studies to be presented at the conference shows how a computer-aided design (CAD) file can create these 2D patterns of slits, while the other study shows how to build electrical components for the robots using self-folding laser-cut materials. The researchers said they came up with designs for resisters, inductors, capacitors and more.
“We have this big dream of the hardware compiler, where you can specify, ‘I want a robot that will play with my cat,’ or, ‘I want a robot that will clean the floor,’ and from this high-level specification, you actually generate a working device,” Rus said.
How about: “I want a robot to destroy my other robot when it becomes self-aware.”
Editors' Recommendations
- 3DMakerpro’s Seal is a pocket-sized scanner to make next-gen precision 3D prints
- The future of making stuff: Inside the evolution of 3D printing with Formlabs
- 3D printing lets hospitals make ventilator substitutes with common equipment
- 3D-printing technique produces tiny, highly detailed objects in seconds
- This 3D-printed four-legged robot is ready to take on Spot — at a lower price